3 Common Issues Caused By Variable Frequency Drives And Best Solutions
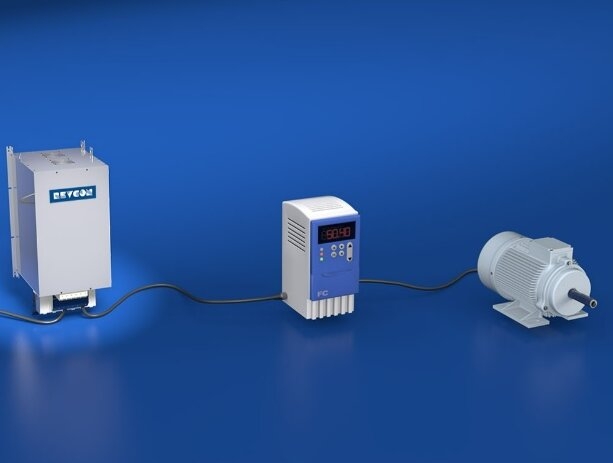
Harmonic filters are an excellent solution for harmonic mitigation and improving the overall power quality of the system. However, when it comes to complicated technology such as variable frequency drives (VFDs), the issues and demands are numerous. The motors working in tandem with the VFDs are often the most affected. In this blog, the focus will be on the 3 main issues caused by VFDs on the motors and the two best harmonic filter solutions to address these problems.
Common Issues Created By Variable Frequency Drives
Excessive Heating In The Motors
Apart from the regular heating losses occurring during the motor operation, there is a prevalence of heating in the stator of the motor, courtesy of non-sinusoidal currents caused by VFDs. In the earlier versions of VFD, this non-sinusoidal current was very significant, requiring motors to be derated. However, more modern versions have almost handled this distortion, except for small fluctuations in frequency.
In these motors using VFDs, the frequency is somewhere in the range of 4 kHz to 16 kHz. Therefore, there is a prevalence of some local heating in the motors.
Issues With Motor Bearings
Motor bearings face additional issues due to a very unique scenario created by their very design. The main culprit behind this is additional heat, which is caused by magnetic flux. During operation, a magnetic flux occurs between the stator winding and the rotor iron. Moreover, the stator winding connects the non-drive end of the shaft to the drive end. Therefore, this magnetic flux travelling through the two ends creates a voltage.
The corresponding current runs through the shaft and the motor bearings. This, in turn, causes more heat in the bearings and leads to their wear and tear. VFDs further accelerate this wear and tear by adding more electrostatic induction between the shaft and the bearings. It leads to a small electric arc that breaks down the film of lubrication on the bearings. Both these phenomena contribute directly to faster breakdown and repair of motor bearings.
VFD Induced Voltage Stresses On The Motor Insulation
The motor insulation is adversely impacted when operated by VFDs, as it is stressed well beyond acceptable levels. This leads to:
Doubling Of Voltage
All AC motors are designed in such a way that the overall magnetic flux density stays optimal at all times. This flux is created by the stator and the rotor, and these parts comprise laminated silicon steel. To maintain this optimum level, the grade of silicon steel must be excellent, and the lamination must be thick. If the flux density is over or under the optimum value, then there are different consequences. If the density exceeds the optimum level, it results in magnetic saturation and leads to a reduction in motor efficiency. Similarly, if the flux density is under the optimum value, then the motor draws in more current to produce the desired level of torque. Therefore, this also negatively impacts the energy efficiency of the motor.
With these issues explored in detail, here’s a look at the two best solutions to tackle these challenges caused by VFDs.
Passive Harmonic Filters
Passive harmonic filters are one of the most common and cost-effective ways to tackle harmonics and their resultant complications caused by VFDs. It comprises a series of inductor-capacitor resonant circuits that tackle a specific frequency. This circuit is connected in parallel to the VFDs to offset its impact. In essence, it has a 3-phase inductor and a 3-phase capacitor. A passive harmonic filter serves 3 primary functions:
- When harmonics match the resonant frequency: If the frequency of the harmonics matches that of the harmonic filter, then it will bypass the distortion to the ground and neutralize its impact in the circuit. For instance, if the harmonic filter’s resonant frequency is 300 Hz, then it will bypass this frequency and make sure that the circuit is free of this particular frequency.
- When harmonics exceed the resonant frequency: In this instance, the passive harmonic filter will perform as an inductor.
- When harmonics are below the resonant frequency: If the harmonic distortion is well below the resonant frequency, then the capacitor part of the filter is activated, offering excellent power quality correction.
Active Harmonic Filters
A more dynamic, albeit expensive, solution to handle harmonic distortion caused by VFDs is active harmonic filters. Instead of creating a filter with a set resonant frequency, active harmonic filters are designed to tackle all types of harmonics. This makes them an ideal solution for light and medium-voltage applications.
Active harmonic filters comprise current transformers and an internal microprocessor, which helps to sense the magnitude of the harmonic distortion. It also consists of IGBTS, multiple capacitors, and inductors. Once the frequency of the incoming distortion is analysed, it generates a frequency that is equal to the distortion, but completely opposite in phase. This helps neutralize the incoming harmonics.
Looking for the right harmonic filter for your needs? Reach out to us at ADM Engineering Inc. today, and our experts will help assess your needs and offer the best possible solution for harmonic mitigation. As a premier distributor of harmonic filters and other power quality solutions, we pride ourselves on the quality of our products and our technical expertise. To know more, contact us at 877-236-8337.
We are currently working on bringing you the full version of our site. Some of the functionalities may be limited at this time.
If you have any questions about the services we offer don’t hesitate call us at +1 (877) 236-8337.